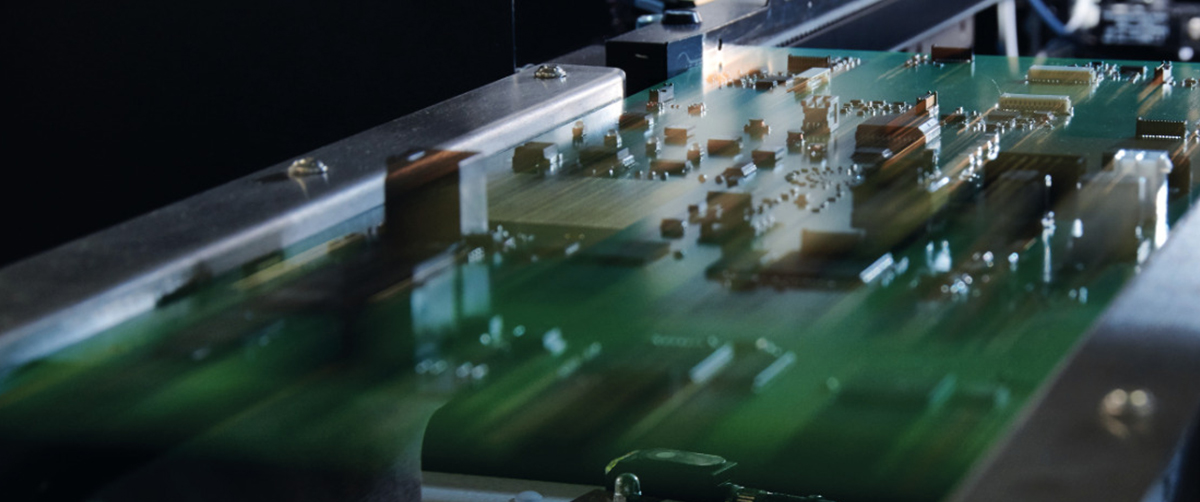
Sistemi raggi x 3D in-line per prodotti di massima qualità
Sistemi di alta qualità per l’ispezione ottica automatica delle schede elettroniche (AOI) offrono rese elevate e collaudi 3D. Per le saldature nascoste, sempre più produttori di elettronica desiderano utilizzare anche sistemi a raggi X in linea (AXI). Si ottengono una veloce gestione delle schede e immagini 3D di elevata qualità. Un esempio è il rilevamento preciso dei void come richiesto dai produttori che utilizzano diodi a emissione di luce (LED) e altre applicazioni BGA, microBGA, etc.
Nella produzione elettronica, quando è necessario esaminare una scheda ritornata dal campo, o ricercare un’anomalia nel processo produttivo o in un prototipo appena sviluppato, è sufficiente l’analisi a raggi X con un sistema manuale (MXI). Il tempo di ispezione con un angolo di penetrazione della radiazione e rivelatore orientabile non è un fattore decisivo. Poiché il sistema MXI è esterno alle linee di produzione, non influisce sui tempi di ciclo.
Tuttavia, se è richiesto un esame ottimale delle saldature nascoste, sono necessari sistemi a raggi X in linea. Esempi tipici di componenti che richiedono questo tipo di apparecchiatura, in cui l’ispezione ottica automatica presenta i suoi limiti, sono QFN e BGA nonché, ad esempio, LED sempre più miniaturizzati.
Gestione simultanea di più schede
I sistemi a raggi X in linea devono segnalare in modo affidabile difetti invisibili all’occhio umano; inoltre, devono essere tenuti in continua evoluzione per stare al passo con le crescenti esigenze di velocità nella produzione elettronica. Ad esempio, oggi è possibile ottenere tempi produzione schede di quattro secondi; di conseguenza, nel sistema 3D AXI possono essere introdotte fino a tre schede contemporaneamente. Se necessario, al fine di evitare che l’ispezione a raggi X rallenti inutilmente il ciclo della linea, è possibile combinare le ispezioni 2D e 2.5D più veloci, con le ispezioni 3D. La tecnologia 3D verrà applicata laddove sarà necessario.
Situazioni di criticità di ispezione
Per una efficace ispezione è spesso necessario disporre di immagini di sezioni delle parti da verificare. È possibile acquisire sia sezioni orizzontali che verticali. A causa della sovrapposizione di componenti, specialmente con schede popolate su entrambi i lati, questa performance è essenziale. In questo caso, con una ricostruzione 3D, tutte le caratteristiche significative possono essere rese visibili in immagini nitide, anche in caso di componenti coperti o schede multistrato. Mentre i dettagli del lato posteriore sono sempre visibili con sistemi a raggi X 2D, la possibilità di creare immagini di sezioni 3D permette di superare tutte queste difficoltà di collaudo. Ciò semplifica notevolmente la generazione del programma di ispezione e consente un’efficace prevenzione di falsi gusti. Per una migliore verifica, la tomografia computerizzata planare di un sistema AXI 3D può essere applicata per generare volumi parziali o completi della saldatura ispezionata, che può quindi essere inclinata, ruotata e ingrandita sul monitor.
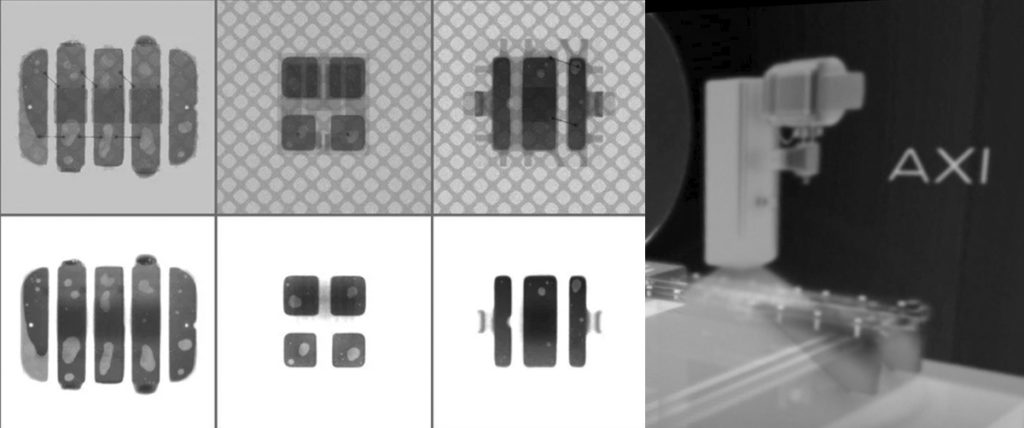
Notare la qualità delle immagini 3D AXI che offre un’eccellente riconoscibilità dei void.
Test di LED con sistemi AXI 3D
Quando vengono esaminati più da vicino componenti LED, è immediatamente evidente che un sistema AOI 3D da solo non è sufficiente per garantire un’alta qualità del prodotto finale. Il collaudo a raggi X risulta il mezzo ideale, in particolare per ispezionare con precisione le saldature nascoste. I LED offrono ai progettisti industriali innumerevoli possibilità applicative, sia per illuminazione interna, esterna (lampioni ecc.) e display; una grande possibilità di soddisfare le loro idee di illuminazione. Il settore automobilistico in particolare ha rapidamente riconosciuto la potenzialità della tecnologia LED, che da tempo si è affermata come uno standard nelle luci dei veicoli, nei lampeggiatori e nei fari. I suoi vantaggi intrinseci includono una lunga durata, elevate rese luminose e un basso consumo energetico.
La dissipazione del calore è una fondamentale caratteristica di qualità
I LED emettono non solo luce, ma anche calore. La rapida dissipazione di questo calore è fondamentale per la loro longevità. L’associazione elettronica IPC non ha specificato nei propri criteri di accettazione alcuno standard per la dissipazione del calore. Queste norme affermano solo che per i componenti connessi a dissipatori di calore sui lati inferiori, i criteri per quanto riguarda questioni legate alla temperatura per le aree nascoste delle saldature, devono essere determinati di comune accordo tra l’utente e il produttore. Per quanto riguarda lo strato di transizione del calore, questi criteri dipendono dal processo e dal design, per cui vanno presi in considerazione le note di applicazione del produttore del componente, la copertura della saldatura, i pori, l’altezza della saldatura, ecc. Non è normale che si formino pori e bolle nello strato termico quando questi tipi di componenti vengono saldati. Tuttavia, in particolare spazi vuoti nei giunti di saldatura (void), possono impedire una dissipazione ottimale del calore tra chip e strati di barriera dei componenti a semiconduttore. La durata (ore di funzionamento), la lunghezza d’onda (colore) e persino la resa luminosa (luminosità) dei LED dipendono fortemente dalla temperatura dello strato barriera.
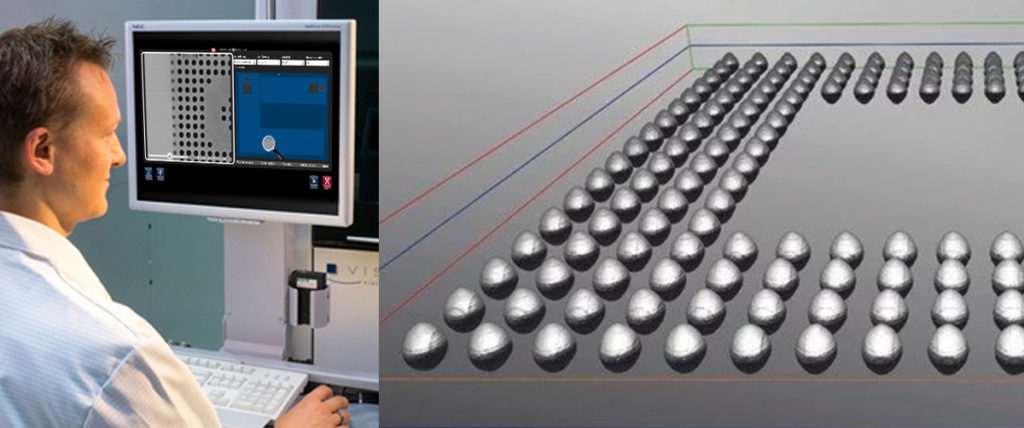
Alta efficienza in base a requisiti rigorosi
Soprattutto nell’industria automobilistica, la produzione e il controllo di qualità di schede con LED sono spesso forniti dagli EMS (Electronic Manufacturing Services). Devono soddisfare i severi requisiti dei loro clienti e allo stesso tempo essere il più efficienti possibile per rimanere competitivi. I titolari di brand specificano in modo molto preciso quale percentuale di void nelle saldature può essere accettata. I forni usati nel processo, camere a vuoto e altri mezzi possono aiutare a prevenire i void. Quelli che si formano possono essere identificati in modo molto chiaro con una radiografia 3D di ultima generazione. Mentre un sistema manuale MXI utilizzato in modo flessibile è adeguato per le ispezioni casuali, una ispezione al cento per cento completamente automatica va eseguita con un sistema integrato nella linea di produzione. In questo modo, i void, anche se nascosti, possono essere completamente registrati e analizzati.
I raggi X e l’ispezione ottica si completano a vicenda
Tuttavia, l’importanza dell’AOI 3D nell’ispezione dei LED non viene affatto messa in discussione. Soprattutto nelle applicazioni automobilistiche, esistono requisiti molto specifici per il posizionamento e l’allineamento dei componenti. Il rilevamento di difetti come la non complanarità dei componenti LED sempre più piccoli dipende da valori di misurazione affidabili. Per supportare la precisione assoluta e la ripetibilità dell’AOI 3D, può essere usato un misuratore di altezza testato con strumenti ad alta precisione da un laboratorio specializzato e certificato. I componenti inclinati possono essere rilevati molto bene con AOI 3D; misurazioni precise si ottengono anche per rotazioni e offset X / Y. Pertanto, l’AOI fornisce un contributo decisivo alla garanzia della qualità.
Ottimizzazione del processo con diversi metodi di ispezione
Da molti anni sistemi 3D AOI e 3D AXI sono stati integrati in modo ottimale in un’unica macchina. Le schede si muovono rapidamente e quasi simultaneamente tra le due aree di ispezione e la combinazione dei due diversi metodi di ispezione può essere opportunamente definita a seconda delle esigenze del momento. Inoltre, un collaudo in rete comprendente i risultati di un’ispezione della pasta saldante (SPI 3D) è un efficace combinazione di dati per un effettivo miglioramento del processo. Nel complesso, le ispezioni di assemblaggio nella produzione di parti elettroniche sono un ottimo esempio di Industria 4.0 implementato con successo. Sistemi SPI 3D intelligenti che comunicano con serigrafiche e dispenser di pasta saldante, dati provenienti da sistemi 3D SPI, 3D AOI, 3D AXI e 3D MXI possono essere rapidamente recuperati dalle stazioni di verifica e riparazione collegate – anche per diverse linee di produzione – e il controllo statistico del processo facilita una panoramica delle distribuzioni dei difetti entro i limiti di tolleranza impostati. L’analisi dei dati provenienti da falsi errori e da difetti reali fornisce preziose informazioni sulla necessità di apportare modifiche nel processo o, ad esempio, se un tipo di componente è particolarmente soggetto a difetti. Inoltre, con l’elevata quantità di informazioni fornite dai sistemi di ispezione per ogni singolo assemblaggio, è possibile tracciare riferimenti incrociati durante l’intera produzione.
Il sistema Viscom 3D AXI X7056-II può essere implementato con il test 3D AOI per una soluzione combinata. Il componente xFastFlow, con il quale è possibile raggiungere tempi di gestione estremamente bassi (fino a quattro secondi), è un’altra importante opzione.